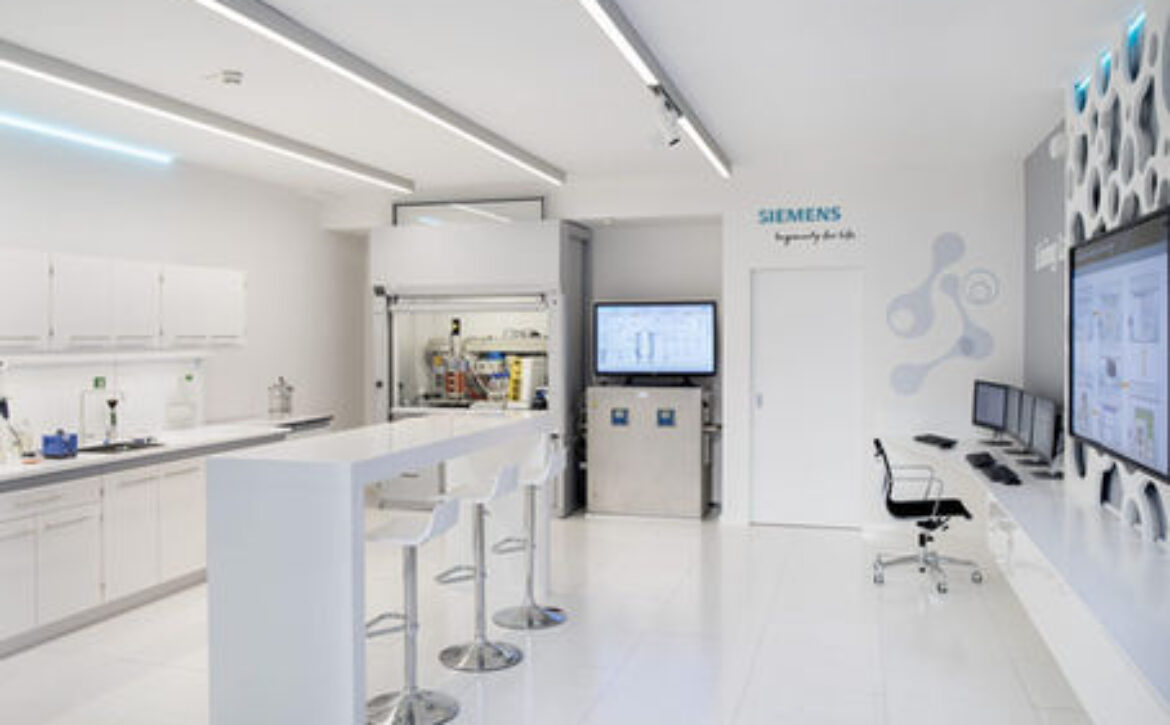
Novasign Soft Sensing Technology at Siemens’ LivingLab
Innovative tools to monitor important upstream bioprocess variables in real-time, such as biomass, are of high interest for manufacturers. Typically, to get these values, a sample must be drawn, processed, and analyzed. These steps lead to an inevitable time delay, which makes this desired real-time monitoring impossible. However, the need for such solutions to meet regulatory guidelines emphasized in the process analytical technology (PAT) guide and the quality by design (QbD) concept is apparent and of high importance. The real-time access to the current biomass concentration and other critical process-related parameters or quality attributes offers many benefits, such as
- valuable information about the bioprocess performance without analytical time delay
- the detection of deviations and the potential to quickly counteract
- the possibility to perform process operations standardized, e.g., transfection or induction of the cells always at the same biomass concentration instead of a pre-determined process time
How can process variables of interest be monitored in real-time?
One of the techniques for real-time monitoring of important bioprocess variables, enabling the mentioned advantages, is called soft sensing. Hereby, a software algorithm is used to identify correlations of process-specific signals, such as critical process parameters (CPPs) derived from hardware sensors (pH, temperature, cultivation off-gas, balances,…), with the desired quality attributes (biomass, product, product aggregation, glycosylation,…). One of the typical first approaches to get such a soft sensor is the utilization of a regression model, also often called data-driven or black-box modeling. By only identifying the correlation of the process data with the variable of interest, the utilized parameters do not have a physical meaning. Therefore, and due to the often-missing causality, these models have the disadvantage of low performance. On the other side, by utilizing a deterministic model (also parametric or white box modeling) in which the parameters do have a physical meaning, causality is given. However, such models only assume a mechanistic trend and, therefore, especially for upstream processes, typically are too simple for the present complexity, also resulting in inaccurate results.
That’s why we applied a hybrid modeling approach instead. By combining both individual approaches into one single model structure we
- make use of different knowledge sources
- obtain a more rational use of the available knowledge
- get more robust and reliable results as achieved by each single model
- offer a solution to handle more complex problems as it is typically the case in bioprocessing
Our in-house case stories, as well as our peer-reviewed publications, articles, webinars, and interviews in the news section cover more details about the various applications of hybrid modeling in bioprocessing (upstream and downstream).
A collaboration facilitates the implementation of our hybrid models in an industrial setup
Siemens, as one of the leading companies for process automation in the pharmaceutical industry, recognized the need and high benefits of soft sensing using hybrid modeling for process monitoring and control. The Siemens LivingLab for digitalization in the process industry offers the possibility to use a professional industrial environment for collaboration and proof of concepts. Both the interest in improving the biomass monitoring of yeast cultivations in the LivingLab, as well as our interest in implementing and testing our models in multiple industrial setups, were high. We started to integrate a simple and fast forward approach within the environment of the Siemens PAT Software Simatic SIPAT. In a collaboration with Siemens, we received data from a two-dimensional DoE from yeast cultivations and built a hybrid model using our hybrid modeling toolbox. After exporting the model, using the .dll file export function, the SIPAT environment offers easy and straightforward implementation of such files. After mapping the modeling parameters with the corresponding OPC parameters in the process control system, we were interested and ready to test the soft sensor performance on new cultivations.
To investigate the accuracy of the predicted biomass values from the soft sensor, two additional cultivations were performed. In a first approach, a cultivation within the design space was performed. The implemented soft sensor was able to accurately predict the actual biomass concentration during the whole cultivation in real-time (Figure 1).

Figure 1. Off-gas, analytical and predicted biomass values for a yeast cultivation (inside the design space) in the Simatic SIPAT environment in Siemens LivingLab
To further challenge the hybrid model, also a cultivation outside of the design space was performed (different medium and starting glucose concentration). Again the soft-sensor proofed its validity to describe the biomass behavior during the cultivation despite the new cultivation conditions (Figure 2). Depending on the model parameter availability, such a Soft Sensor can also have a predictive nature. If the hybrid model is solely created on a design space using controllable process parameters, the response variable of interest (here the biomass) can be predicted in a multi-step ahead approach for any future time point.

Figure 2. Off-gas, analytical and predicted biomass values for a yeast cultivation (outside the design space) in the Simatic SIPAT environment in Siemens LivingLab. A different medium and a different glucose concentration was utilized to test the soft sensor performance
The combination of the impressive SIPAT environment and the possibility to quickly implement powerful models in combination with our hybrid model structure created a valid showcase, which can be implemented fast and easy at the pharma customers’ site. We are looking forward to continuing this journey not only with additional end-customers for the industry but also with other real-time systems. If you are interested in testing this approach, please get in contact with us. We are confident that more people will discover the high benefits of this hybrid soft sensor technology and will make use of it.